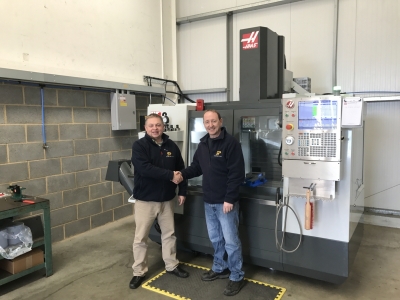
The new building—Unit 8—is adjacent to existing Straightpoint Units 10 and 9; it will primarily be utilised as a machine shop, where the force measurement, load monitoring and suspended weighing load cell equipment supplier will bring in house the manufacture of non-standard equipment. The expansion follows the arrival of Mike Neal, product sales engineer, who will drive increased sales of custom products.
David Ayling, director at Straightpoint, said: “There’s a cohesion to recent developments as we implement a vertical manufacturing strategy centred on our non-standard range. Combining a dedicated resource for sales with a machining expert of Marcus’s calibre, who has state-of-the-art equipment at his disposal, sees us take multi-level control of the supply chain. We’ll continue to use local machine shops for standard equipment, with whom work can be booked months in advance, but only with an in-house resource can we transform the speed and efficiency with which we deliver custom below-the-hook solutions.”
Straightpoint has sourced key equipment for Unit 8 from Haas Automation, an American machine tool builder headquartered in California, which has supplied the centrepiece VF-2 CNC (computer numerical control) milling machine and TL-1 CNC lathe. A Bridgeport manual turret mill, Colchester chipmaster lathe, Sealey band saw and hydraulic press are just some of the additional tools that will complete the comprehensive machine shop.
MacDonald, who brings three decades of relevant experience to the role, most recently overseeing a team of 13 engineers, said: “The position appealed to me because it represents an opportunity to combine my expertise with a return to a core focus on CNC and manual machining, which I am passionate about. We have consulted with Haas and utilised the space available to provide the company with machining capability that will revolutionise supply of non-standard and other SP equipment.”
Loadpins, compression load cells and shackles are likely to be among the first custom products to be machined in the new workshop, as the subsea, marine, offshore and other sectors look set to benefit from faster turnaround on orders. MacDonald will both respond to demand generated by Neal and produce stock in line with industry trends.
Alfie Lee, operations director; and Roshan Divakaran, design engineer, have also been integral to the on-boarding of personnel and equipment. The latter has been providing support on CNC software and programming, for example.
Straightpoint plans to recruit an apprentice to the new machine shop, who will be given the opportunity to follow in the footsteps of Ayling and MacDonald. The pair first met at the age of 16 when they were apprentices at Britax Wingard, a Chichester-based motor parts manufacturer. “Opening the door to the next generation as a by-product to our ongoing expansion makes our growth all the more rewarding,” Ayling concluded.