News & Case Studies
- Details
- Written by Tanya
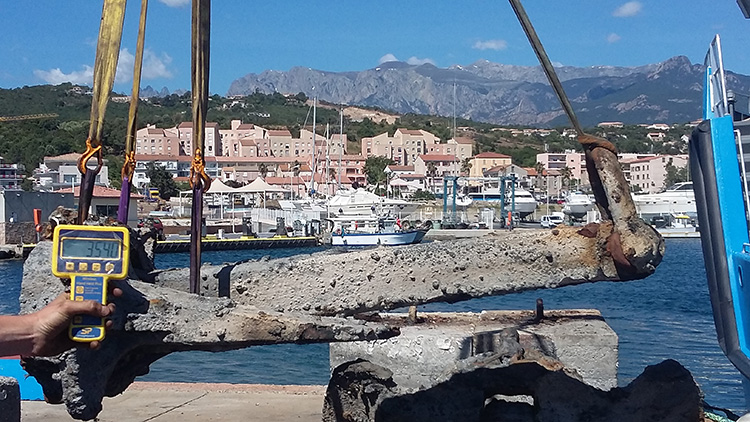
French maritime engineering specialist Iroise Mer, based in Brest on the country’s northwestern coast, used a 50t Straightpoint Radiolink plus (RLP) load cell during a refit of a tanker mooring system located 500m off the Corsica coast, recently.
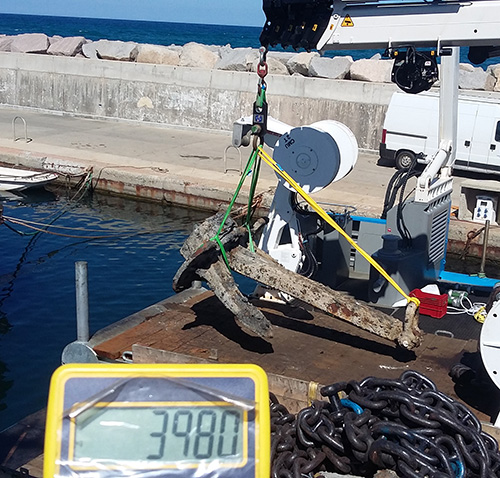
The RLP was positioned between the anchor line (or chain) and the towing cable on a vessel, attached with two Green Pin shackles. Straightpoint does have a product for measuring tension on lines, the Running Line Dynamometer (or TIMH), specifically built with dockside, marine, offshore, towage and salvage applications in mind.
However, as David Mullard, SP business development manager, explained, “the TIMH wouldn’t have been suitable because anchor chain was being used rather than wire rope. Wire rope can bend, allowing it to pass through the sheaves of the TIMH so that a tension measurement can be calculated. The large dimension chain wouldn’t have allowed the same thing to happen,” he said.
Pierre Recoules, project manager at Iroise Mer, who was aboard the nearby boat, took Readings on a Handheld Plus. He explained that safety was improved, as there was no need to put personnel in the towing line where the load cell was attached.
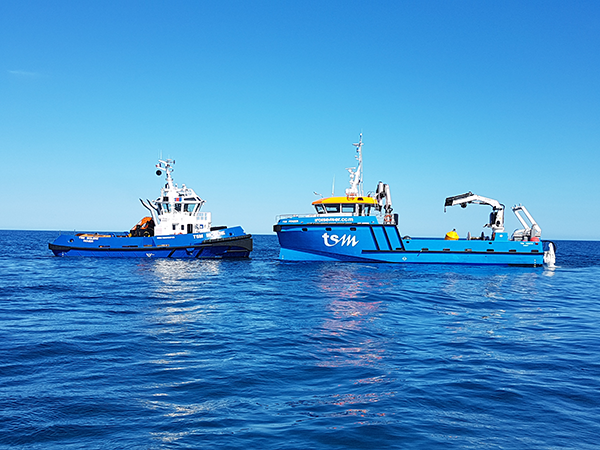
Mullard added: “The application shows how the RLP is well suited to any form of weighing, tension measuring and monitoring applications, combining simple operation and strong wireless connection. Waterproofing wasn’t an issue as the RLP stayed clear of the water but it could have been left permanently rigged with no problems.”
The new anchors and chains were manufactured in France before being shipped to Corsica, a mountainous French island that is actually close to the west coast of Italy. The jobsite was off the coast of Solenzara on the island’s east.
Iroise Mer, founded in 2002, has been part of the Thomas Services Maritimes (TSM) group since 2013. Iroise has a fleet of six vessels, ranging from 10m to 41m in length, all of which boast cranes, winches and shallow drafts, suiting them to lifting and towing projects. TSM has a fleet of 20 additional vessels, predominantly tug boats for harbour towing operations.
Two vessels, TSM Molène and TSM Penzer, were used for the Corsica project, which are 21m and 27m in length respectively. Tension was applied via the vessels’ thrusters. Recoules led a 10-person team, who completed the work inside a calendar month.
Straightpoint serves the French marketplace through its local distributor Traction Levage (http://www.traclev.com), which has six facilities across the country.
- Details
- Written by Tanya
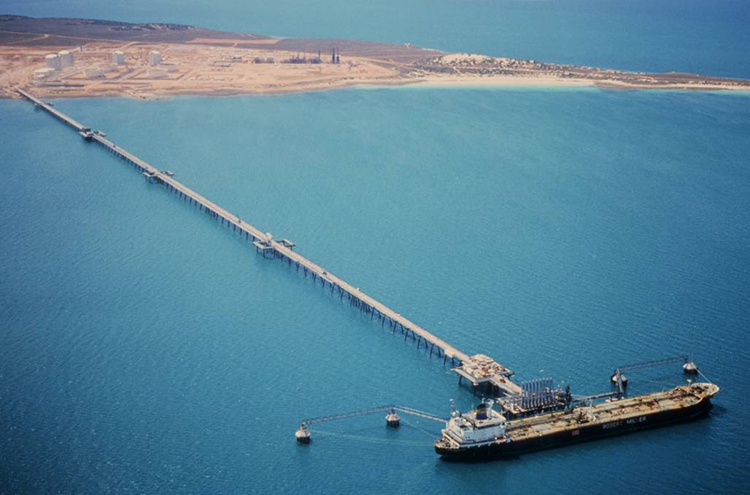
Dynamic Rigging Hire (DRH) supplied a 25t Wireless Loadshackle and a 20t girder trolley, which combined with a 16t air hoist, for remediation work beneath a fuel terminal jetty at Port Bonython in South Australia. The deepwater port is adjacent to Point Lowly in the Upper Spencer Gulf region, the westernmost of two large inlets on the southern coast of Australia.
Port Bonython is a hydrocarbon processing plant and is named after Santos’ founding chairman, John Bonython, Opened in 1982, liquefied petroleum gas (LPG) production commenced in 1984 and with it the first export to Japan. The inherent nature of the site presented challenging conditions for DRH, which collaborated with fellow Victoria-based company Hoisting Equipment Specialist (Vic) Pty Ltd (HES) to deliver the three-week hire solution.
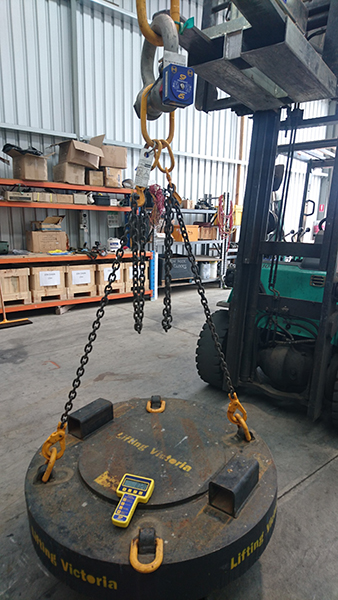
Ross Johnson, general manager at DRH, said: “Integral to our service is delivery of the best solution based on a customer’s requirements. We were indebted to Dean Nelson [managing director at HES] and his team, who were able to leverage their position in the marketplace to help us assemble the right package for the Port Bonython corrective work.” Nelson is also a director of DRH, Johnson pointed out. The Port Bonython hire project served as an exemplar of DRH’s strict policy to verify all force measurement, load monitoring and suspended weighing load cell equipment upon its return from site, before redistribution to other projects.
DRH used a steel test weight and a 3.5t capacity Mitsubishi lift truck to inspect the 25t Wireless Loadshackle. Johnson said: “It’s vitally important to ensure the load cell is functioning correctly with no signs of it being overloaded or other visual defects. The load shackle is exceptionally accurate; during the inspection process we had only 1,020kg of weight on a 25t device so the loadings were in the lower range of the load cell.”
- Details
- Written by Tanya
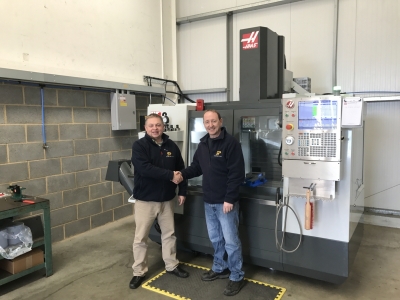
The new building—Unit 8—is adjacent to existing Straightpoint Units 10 and 9; it will primarily be utilised as a machine shop, where the force measurement, load monitoring and suspended weighing load cell equipment supplier will bring in house the manufacture of non-standard equipment. The expansion follows the arrival of Mike Neal, product sales engineer, who will drive increased sales of custom products.
David Ayling, director at Straightpoint, said: “There’s a cohesion to recent developments as we implement a vertical manufacturing strategy centred on our non-standard range. Combining a dedicated resource for sales with a machining expert of Marcus’s calibre, who has state-of-the-art equipment at his disposal, sees us take multi-level control of the supply chain. We’ll continue to use local machine shops for standard equipment, with whom work can be booked months in advance, but only with an in-house resource can we transform the speed and efficiency with which we deliver custom below-the-hook solutions.”
Straightpoint has sourced key equipment for Unit 8 from Haas Automation, an American machine tool builder headquartered in California, which has supplied the centrepiece VF-2 CNC (computer numerical control) milling machine and TL-1 CNC lathe. A Bridgeport manual turret mill, Colchester chipmaster lathe, Sealey band saw and hydraulic press are just some of the additional tools that will complete the comprehensive machine shop.
MacDonald, who brings three decades of relevant experience to the role, most recently overseeing a team of 13 engineers, said: “The position appealed to me because it represents an opportunity to combine my expertise with a return to a core focus on CNC and manual machining, which I am passionate about. We have consulted with Haas and utilised the space available to provide the company with machining capability that will revolutionise supply of non-standard and other SP equipment.”
Loadpins, compression load cells and shackles are likely to be among the first custom products to be machined in the new workshop, as the subsea, marine, offshore and other sectors look set to benefit from faster turnaround on orders. MacDonald will both respond to demand generated by Neal and produce stock in line with industry trends.
Alfie Lee, operations director; and Roshan Divakaran, design engineer, have also been integral to the on-boarding of personnel and equipment. The latter has been providing support on CNC software and programming, for example.
Straightpoint plans to recruit an apprentice to the new machine shop, who will be given the opportunity to follow in the footsteps of Ayling and MacDonald. The pair first met at the age of 16 when they were apprentices at Britax Wingard, a Chichester-based motor parts manufacturer. “Opening the door to the next generation as a by-product to our ongoing expansion makes our growth all the more rewarding,” Ayling concluded.
- Details
- Written by Tanya
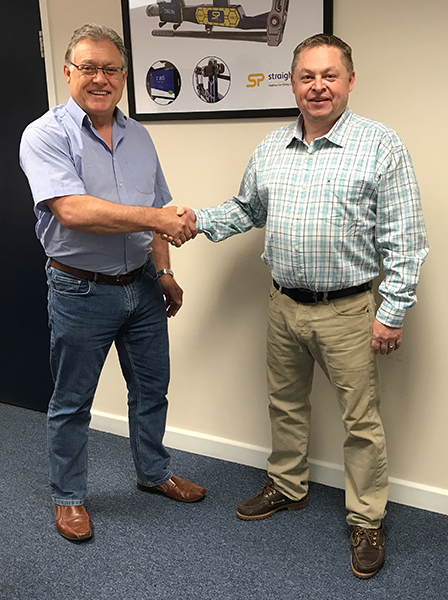
Neal, who joined the company in mid-April 2017, will aim to further increase the lead conversion rate related to the range by qualifying enquiries and generating proposals in addition to focussing on liaison and follow-ups with existing and prospective customers.
He said: “As a part of my previous roles in sales of standard weighing products there was a frequent requirement to configure special application solutions based on staple weighing components, so the process of producing bespoke quotations is already well understood.”
David Ayling, director at Straightpoint, said: “I make no secret of the fact that we want to increase our conversion rate on non-standard products to somewhere close to that of our standard range. Mike brings a wealth of experience and much energy to the role and I am confident he will meet and exceed the short-term and long-term targets we have set.”
Neal’s previous employers worked in industrial weighing within the pharmaceutical, chemical and food / beverage industries. He said his immediate challenge is to apply his expertise in weighing and other similar technologies as it pertains to these sectors in the lifting equipment marketplace and the SP range of solutions.
He explained: “I’m looking forward to getting up to speed with the hoist and heavy-lift Industries, in particular. As is the case when offering any non-standard product, a comprehensive understanding of the application and requirements of the solution are required, so the quicker I can get to that stage the more effectively I will be able to start working towards our longer-term goal of becoming the go-to company for bespoke solutions as an increasingly informed marketplace seeks our consultation and technologies.”
Ayling has set a target percentage of leads to convert, based on a typically systematic strategy and data gathered from the standard product division. Neal welcomed the challenge and believes a new dedicated resource can exceed expectations.
He concluded: “I have been aware of Straightpoint’s products for over 15 years and I’m exciting about finally representing them at a stage of my career where a new challenge has really whet my appetite. I look forward to starting the dialogue and delivering non-standard SP products to the multitude of industry sectors in which they can be applied.”
- Details
- Written by Tanya
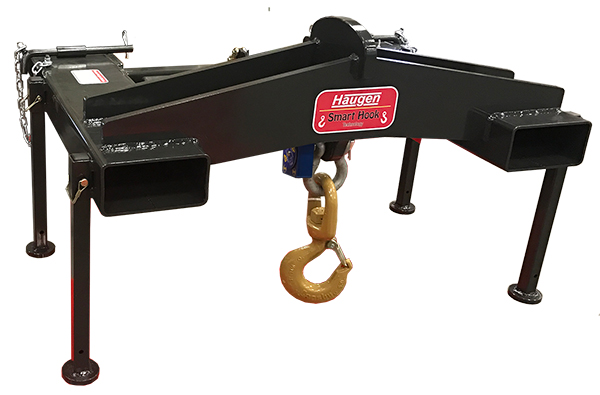
Forklift and telehandler accessories manufacturer Haugen Attachments is offering the innovative Smart Hook, an attachment that incorporates a 7.2-ton (14,000-lb.) capacity Straightpoint load cell.
The 225-lb. Smart Hook can be easily attached to all kinds of telehandlers, giving end users a Crosby swivel hook that incorporates a wireless load shackle positioned at the center of a 42-inch wide and 36-inch long attachment; the attachment holds the lifting hook at 24 inches on center. Four legs act as storage stands to keep the load cell off the ground, which can be removed or left in place during use.
Straightpoint’s wireless load shackle is primarily used in low headroom applications. Boasting an anodized, aluminum electronics enclosure, an internal chassis provides IP67 / NEMA6 environmental protection even with the battery cover missing. The Smart Hook concept utilizes the technology to measure loads and ensure telehandlers are not used beyond their rated capacities. Operators typically read data via a device in the cab.
Jeff Haugen, general manager, Haugen Attachments (the company is owned by his mother, Carol Haugen, CEO), said: “The beauty of the system is that there is no installation required, allowing the unit to be moved from one machine to another in seconds. Further, it gives an accurate load measurement without confusing set-up or programming. It is a safe and simple solution.”
Haugen explained that the product was conceptualized in response to increased use of telehandlers on U.S. jobsites and the lack of another load measuring device in the marketplace. The company has been manufacturing hooks without load cell technology for many years. The new hook has proved popular with both sale and rental markets; the latter has been keen to capitalize on its interchangeability and divide rental rates over multiple applications.
Haugen said: “Telehandlers have the ability to lift and extend out a load. They have load charts for each position but in most cases the end user does not know the weight of each load they are lifting, which should be confirmed before the operator extends out the boom. The Smart Hook allows the operator to weigh the load and consult their load chart before starting a lift.”
Haugen offers the product in different sizes, with the most popular being its 14,000-lb. (7-ton) capacity unit. Much of the telehandler marketplace is covered by the 8,000-lb. to 12,000-lb. capacity equipment range. However, Haugen has the capability to manufacture the Smart Hook up to 30,000-lb. capacity.
David Ayling, director at Straightpoint, said: “The Smart Hook concept leverages the inherent benefits of the wireless load shackle in limited headroom applications. We’re always excited to see innovative use of our technologies and the Haugen team has opened up a new marketplace for the product. As industry trends suggest there will be continued increase in telehandler utilization in North America, it’s exciting to be involved with a product that enhances safe use of the equipment across varied agriculture and industry sectors.”
Operators drive telehandler fork tines onto the Smart Hook; it is secured into position with pins behind each tine with an additional safety chain and hook, Haugen explained.