News & Case Studies
- Details
- Written by Tanya
Straightpoint Load Cells Weigh Hulking Flare Stack
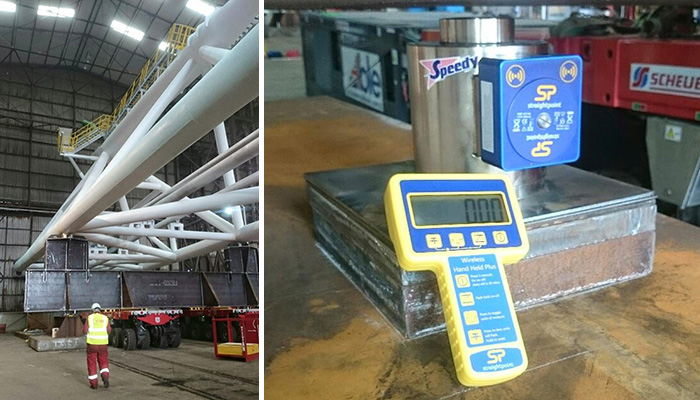
Speedy Services used load monitoring and suspended weighing load cell equipment from Straightpoint to weigh and calculate the centre of gravity of a 298t flare stack bound for a BP oil rig in the North Sea.
Speedy utilised four 150t wireless compression load cells and wireless centre of gravity software with supplementary SW-HHP handheld displays.
The load cells were chosen for a number of reasons, chiefly because they offered an accuracy of +/- 0.5%, compared to other units that were considered which provided a wider margin of +/- 1%.
Accurate measurement of the stack was so critical that weighing was carried out under a shelter to prevent rainwater impacting the calculations. The fabrication shed in Aberdeen, Scotland had to be large enough therefore to house the 98m-long flare stack. It took approximately five hours to complete the load out.
Terry Bide, depot manager at Speedy Services, was responsible for sourcing suppliers for the project that could manufacture to the specified tolerances and deliver to the stringent timescales enforced by the oil and gas giant.
He said: “The weighing technology was integral to the safe completion of a job that required extensive lift planning and top level expertise from the lifting industry throughout. It would have had a massive impact when the unit is finally installed to find the weight or centre of gravity was even slightly incorrect and the crane onsite rendered unsuitable.”
He added: “Thus, the contractor, working on behalf of BP, specified at the outset that they required highly accurate weighing technology. The load was nearly 90m-long, while the average for a flare stack of this kind is much smaller, say, 60m. The success of the project was owing to the industry-leading technologies and expertise employed.”
Self-propelled modular transporters (SPMT) were used to jack the flare stack prior to load out. Flare stacks are sometimes called gas flares and are commonly installed as combustion devices on industrial plants such as petroleum refineries.
An SPMT was positioned at each end of the stack beneath supports that secured the flare in position. The load cells reported live information from four pick points to a handheld device, where operatives monitored the weighing procedure from a safe distance.
Bide concluded: “Given the critical role played by the weighing and other equipment on what was a successful project, I wouldn’t hesitate to utilise the technologies again for future oil and gas or other applications of this scale.”
The stack remains on the Aberdeen dockside awaiting completion of its accompanying module before transportation to the North Sea site.
- Details
- Written by Tanya
New Load Test Software Produces Certification Onsite
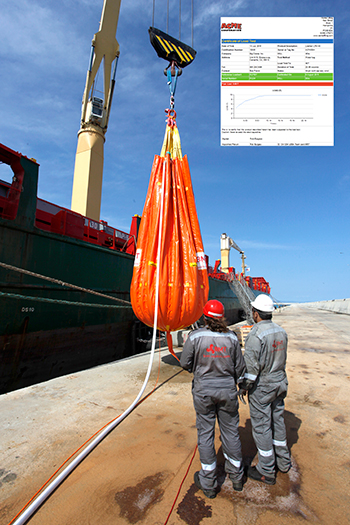
Proof Test plus records data gathered by a Radiolink plus load cell, load shackle or compression load cell, for example, which can be printed out directly as a PDF report or electronically transmitted and stored, along with a certificate of testing. The software can also produce graphs charting data from the load versus time throughout a test.
The system, offering 700m (2,300 feet) range, will be used in a myriad of load testing applications, including cranes with water bags or block weights; tugs and bollards; pad eyes or flypoints (marine industry); crash barriers; construction equipment; below-the-hook equipment; and more.
David Ayling, director of Straightpoint, said: “During our research we found an end user who conducts load tests on a regular basis and he was hand-writing 30 certificates a day. His drawn out routine involved taking them back to an office, where an admin team would enter the data, before they were eventually mailed back to the client.”
He added: “Not only did the archaic process mean someone was waiting for days, weeks even, for load test results, the system wasn’t flawless as mistakes could be made during recording the data manually on site or when information was entered at the office. Now, in theory, a crane rigged with force measurement equipment for a load test can produce certification and then lift a load immediately.”
Straightpoint already provided a series of software products, including a wireless centre of gravity tool, multiple wireless control system and desktop controller, but the Proof Test plus (or SW-PTP) is a tailored technology specific to load tests, compatible with the manufacturer’s force measurement, load monitoring and suspended weighing load cell equipment that is utilised for load testing in the field on a daily basis.
The launch of Proof Test plus is another example of Straightpoint processing market intelligence from both sides of the Atlantic and delivering a state-of-the-art solution. Houston, US-based Aaron Orsak, technical sales engineer; and Dave Mullard, business development manager, who reports to Hampshire, UK headquarters, reported growing demand for dedicated load test software to Sarath Chandran, project engineer. He led a subsequent eight-week development programme that culminated in this week’s launch of the game-changing technology.
Ayling said: “We had existing technologies and systems that could essentially provide the same information but there was a gap in the market for a dedicated, niche load test product that provides accurate, fast information and creates an audit trail. The speed and efficiency of the certification process also enhances the professionalism with which users can serve their customers at the sharp end of the industry.”
Additional key features include free entry fields, to note wind speed and sea states, for example, and log data at speeds up to 200Hz.
- Details
- Written by Tanya
Straightpoint Makes Marquee Acquisition of Load Cell Heavyweight
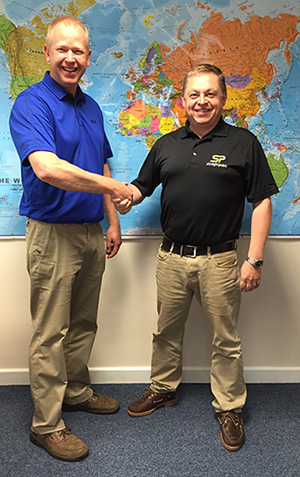
Wille, who is well-known to end users and distributors across North America having sold the wares of another supplier, cited Straightpoint’s breadth of product offering as the main reason for joining the company.
He said: “I am confident that in this new position I will be able to offer dealers and users of the equipment 35 to 40% more product variety than what is being tabled by other suppliers. Combined with my market knowledge and understanding of the diverse applications where it is important to understand the weight of load, having such an extensive range at my disposal is very exciting.”
Wille highlighted Straightpoint’s ability to react to industry to provide innovative solutions, which he noted had recently manifested itself in extending the range of its wireless products to nearly 2,300ft, in addition to new products for explosive environments, the Running Line Dynamometer (part of the manufacturer’s tension in motion range), load pins and load shackles.
David Ayling, director of Straightpoint, said: “It is hard to overstate the significance of Wayne’s arrival at the company and the impact it could have on the load cell sector. For many years, he has been at the coalface of our industry and combining his attributes with the best tools available is a mouthwatering prospect.”
Wille has monitored development of the marketplace over three different decades and believes his new employer can pioneer further progression in two areas that he has seen evolve the greatest during that time—data transmission and capacity.
As he pointed out, Straightpoint’s wireless technology allows antennae free data transmission and can be connected to the latest Internet of Things technology, while the Radiolink plus is supplied with an update rate of 3Hz and can be easily configured to run at speeds of up to 200Hz. Data is transmitted wirelessly utilising the latest in IEEE 802.15.4 (2.4 GHz) technology.
Wille said: “This industry has gone beyond the simplicity of what is being lifted and how much it weighs. While those core principles remain, equal gravitas must be placed on data collection and the speed at which we can transfer accurate information from below-the-hook to professionals overseeing the lift. That’s in addition to the constant challenges presented by the staggering capacities that modern day equipment can lift and move.”
Ayling concluded: “Such is the scale of growth potential that Wayne brings to an already high performance North American operation, we have also had to prepare our UK-based departments to be dynamic in response to an anticipated spike in demand. We are poised for a very exciting second half of the year.”
- Details
- Written by Tanya
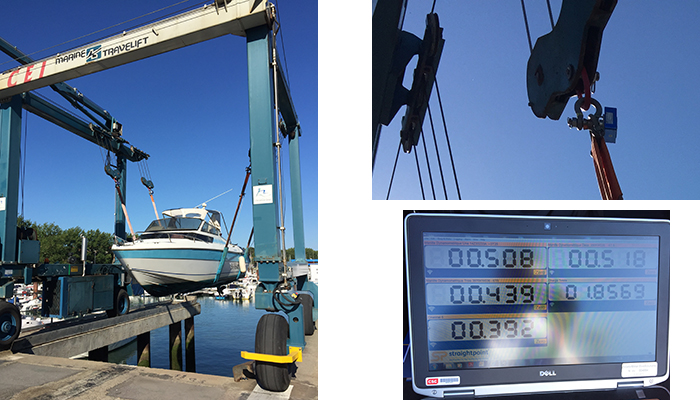
Press Release: 7 July 2016
French Port Upgrades Weighing Technology on Boat Hoist
The Brise Lames marina in Anglet, southwest France, has installed four wireless load shackles and a multi-load cell monitoring and logging system from Straightpoint onto a 25t marine boat hoist.
The hoist, manufactured by Sturgeon Bay, Wisconsin-based Marine Travelift Inc., already possessed weighing technology but it has been in operation since 2002 and the end user required more accurate measurement of vessels, which are typically removed from water for maintenance.
Straightpoint’s French distributor, Traction Levage, provided the solution in four 6.5t wireless load shackles, which were an ideal fit with two pick up points on either side of the boat hoist that moves on four rubber tyres beneath uprights in the corners of the lifting machine. Installation involved integration of two shackles onto both ends of two flat slings, which pass under boats. The logging system provides simultaneous data and the ability to print load reports, whilst confirming mass and centre of gravity.
Dave Mullard, business development manager at Straightpoint, said: “It was very important for the end user to have accurate load information. Not only is this key to the ongoing safety of boat lifts to prevent overload situations, but also they charge their customers based on weight of vessel. The heavier they are, the more expensive the cost of lift, for example. Now, the boat hoist operator can implement an accurate billing system and give customers access to the data upon which those calculations are based.”
Mullard added that the wireless load shackles were ideal for permanent installation in an outdoor environment, explaining that contained within the aluminium enclosures is a new internal chassis providing IP67 / NEMA6 environmental protection even with the battery cover plate missing.
He said: “The installation demonstrates the suitability of Straighpoint systems to Marine Travelift and other boat hoists of varying type and capacity, to the point where they could almost become ubiquitous in such applications. We will work closely with Herve Capdeville, of Traction Levage’s Bordeaux facility, who facilitated this installation, and other distributors around the world to that end.”
The 25t unit, which operates at a facility in Port de Bayonne, is from the manufacturer’s low capacity range to 100 tons, but the maximum capacity of its C-Series goes up to 1,200 tons. Straightpoint wireless load shackles are available from stock in capacities from 3.25t to 500t, meaning similar ease of installation can take place even on the largest models.
- Details
- Written by Tanya
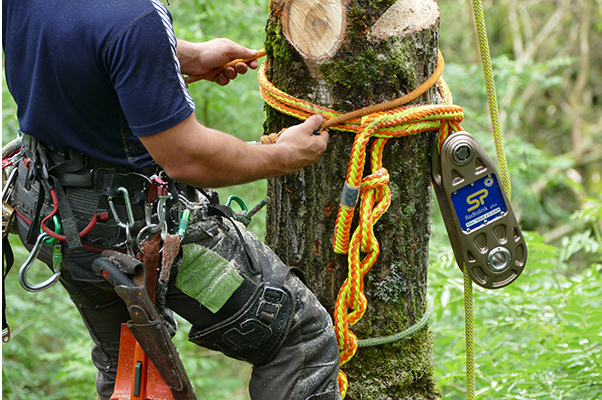
Tree surgeons and other professionals from the arboriculture industry have embraced a new technology that measures the shock load and weight of branches as they are cut during felling or maintenance.
The Impact Block load cell is manufactured in partnership with tree safety equipment pioneer DMM and contains electronics and software from force measurement, load monitoring and suspended weighing load cell equipment specialist Straightpoint. The product was commissioned by a tree maintenance company in the sector.
The industry has acknowledged that the Impact Block can fill gaps in knowledge about the forces put through rigging equipment and the weight of loads as they are cut away from trees. It can become as important as a training device as it is a practical onsite tool for the sector.
Unlike crane-related or other typical rigging scenarios, in tree applications professionals do not always have an anchor point above the lifting point. If only the stem and canopy of a spruce tree remains, for example, a rope break may have to be attached to the bottom of the tree from where a rope and pulley will connect to the piece being cut.
As cuts are made, wood is essentially thrown into the rigging from above. This is in stark contrast to crane lifts, where the hook is typically positioned directly above the mass of the load being rigged and lifted. In the lifting and material handling business, testing is also commonplace but this is frequently impossible in the tree sector because of logistics and the damage such tests could cause to soil and surrounding areas, which in themselves are of critical importance to the health of the tree and subsequent maintenance operations.
The aesthetic curves of the Impact Block combine with strength and durability to ensure a rope-friendly surface. Utilising wireless dynamic load monitoring electronics and strain gauge technology, real time data can be displayed on a handheld controller, tablet or laptop at speeds up to 200Hz. Importantly, this eliminates the estimation work that often goes into arborist applications.
The UK’s Heath and Safety Executive (HSE) was involved in a research programme in 2008, which opened many people’s eyes to the extent of the forces generated and the requirement to more scientifically and accurately research such activity. The launch of the Impact Block places a yardstick in the progress of the sector’s technological advancement and many are campaigning for its widespread use.
One arborist said: “To be able to demonstrate real time shock load data to a group of students is incredibly powerful. Furthermore, we can use the technology to delve deeper into dynamic load situations by researching where forces on the anchor point are at their greatest, while investigating what is happening to the rigging before and after that moment.”
He added: “We need to demonstrate these numbers to existing arborist professionals and those new to our industry. Unless we understand the forces, we can’t understand the safety factors. We frequently work in close proximity to other trees, buildings and infrastructure. The consequences of a lack of understanding about the loads and the forces they place on rigging equipment can be catastrophic if not researched extensively.”
It is anticipated that the Impact Block will be of particular interest to tree professionals in North America, where utilities equipment and power lines are more commonly above ground. Uptake is also expected from large contractors and those engaged in arborist-related training.
Straightpoint director David Ayling said: “The technology built into the impact block is based on technology that has proven its accuracy and durability in a myriad of demanding applications in the lifting and other industries, largely based on the blueprint of our most popular product, the Radiolink plus load cell. The conception of the Impact Block again demonstrates our ability to apply our force measurement expertise to industries looking to use their own state-of-the-art hardware and equipment to raise safety levels and improve best practice. We look forward to a long and fruitful partnership with the tree maintenance sector.”